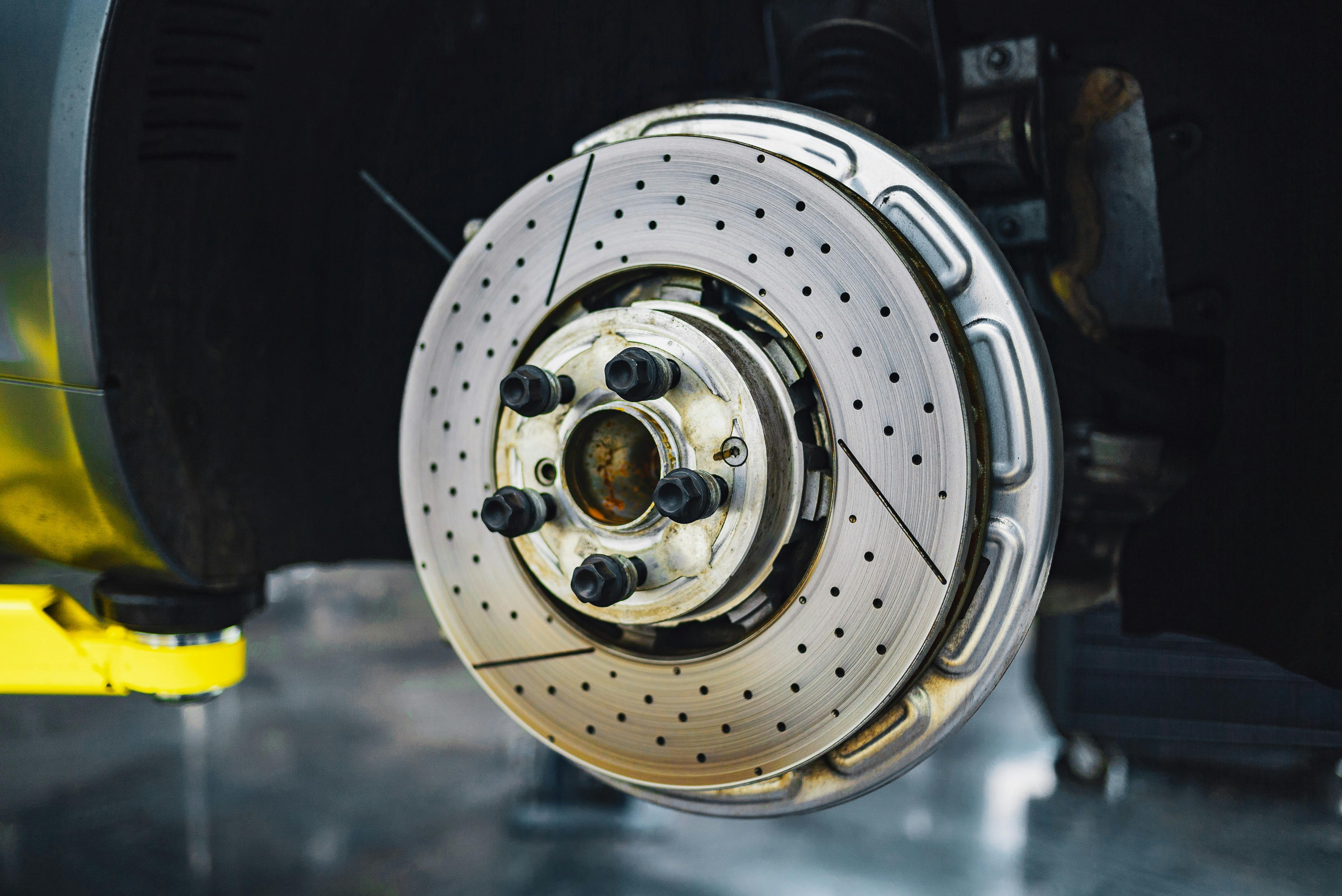
Surface hardening of steel and its applications
admin
- 0
Surface hardening is also known as surface hardening, which is a method that produces a tough layer on the metal surface by some other metal alloy that is mainly more durable. Low carbon steel is often covered with a stronger, more durable metal alloy. This surface hardening process is normally done after the part is in its final shape. The content of hardening elements of the bars, which are subsequently used in pattern welding or other similar processes, can also be determined. The procedure is generally followed for parts that generally require a more wear resistant surface that is internally strong to withstand heavy loads.
In the case of high carbon steels, when hardened, the hardness penetrates the core and causes brittleness. This is the procedure in which the surface of the metal is chemically changed by starting with a high carbide or nitride content. The core of the material is not chemically affected. As it is heat treated, the high carbon surface reacts to hardening and the core becomes hard. Components that undergo this cementation process include: universal joints, camshafts, linkage components, drive sprockets, shafts, and shafts. In many of these cases, the surface that requires hardening is selectively hardened, leaving most of the part in its original state.
Applications of cemented components:
1. Power generation: Case-hardened components are typically used for sprockets and other large components that have to withstand both wear and stress, such as in hydroelectric power plants, steam turbine gears in power plants, or drilling rig propellers and wind. turbine generators.
2. Transportation: Generally, in all motor-driven vehicles, these hardened components are used, including race cars, trucks, or even ocean-going vessels.
3. General Mechanical Engineering: Steel rolling equipment, heavy duty transmissions, forging presses, earth moving equipment and heavy construction cranes require cemented materials. For these applications, the hardened materials used exhibit a combination of strength and fatigue resistance.
4. Another common application on which the process is carried out are screws, especially self-drilling ones. To drill, the forming threads and the drilling tips must be harder than the material to be drilled, so the process is carried out on screws. The cutting and threading of other materials such as steel is also carried out.
Steel Case Hardening
In the metal skin, carbon is penetrated to create mild steel that has an outer shell with carbon than the core. The mild steel is then heated to a particular temperature until it turns bright red. For the formation of the outer surface, mild steel is immersed in a carbon compound, however, it requires several immersions and reheats. This procedure will produce the skin above the metal that is rich in carbon.
The main forms of this process are:
1 cyanide
2 nitriding
3 carburetion